Designing and putting in a mezzanine entails a structured process to make certain that it meets the particular needs of your facility, complies with safety rules, and is built to last.
Assessment and Planning:
Identify your storage or space wants, price range constraints, and project targets.
Assess the available area, ceiling peak, and layout of your facility.
Determine the meant use of the mezzanine (storage, office area, production, etc.).
Regulatory Compliance:
Check local constructing codes and regulations related to mezzanine installation. Regulations might embody load capability, structural integrity, and security options.
Design:
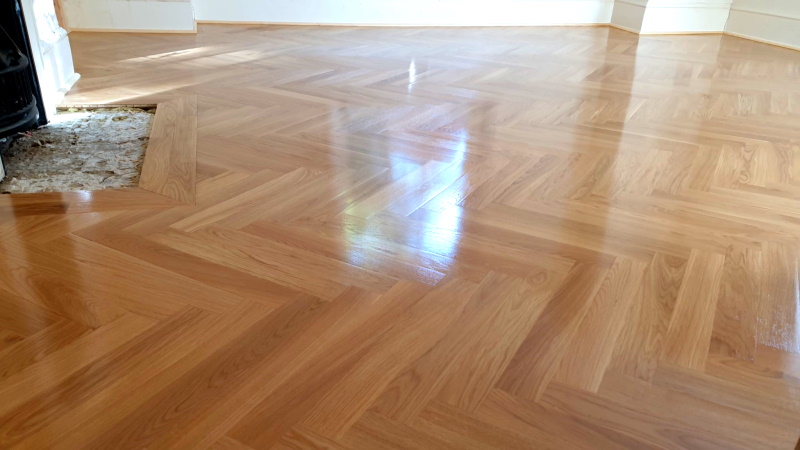
Work with an architect, engineer, or mezzanine design specialist to create a design that meets your wants and complies with regulations.
Determine the scale, load capability, and structure of the mezzanine.
Choose supplies for the structure and flooring, which can include metal, concrete, or other materials.
Plan the location of staircases, handrails, and other safety options.
Consider how the mezzanine integrates with your present infrastructure and workflow.
Permits and Approvals:
Obtain any necessary permits or approvals from native authorities. This could include building permits, zoning variances, and security inspections.
Fabrication:
Fabricate the structural parts of the mezzanine in accordance with the design specifications. This might contain welding, cutting, and assembling metal beams, columns, and other parts.
Installation:
Install the mezzanine components in your facility. This typically includes assembling the construction, putting in the flooring, and integrating safety options.
Safety Features:
Ensure that safety options similar to guardrails, handrails, and staircases are correctly installed to meet safety rules.
Access and Egress:
Design and set up safe and convenient entry points to the mezzanine, corresponding to stairs, ladders, or elevators.
Quality Control:
Conduct high quality management inspections to verify that the mezzanine is constructed to the specified design and safety requirements.
Load Testing:
Perform load testing to make sure the mezzanine can support its meant weight capacity.
https://qcflooringmiltonkeynes.uk/best-lvt-flooring-milton-keynes/ :
Maintain detailed documentation of the mezzanine's design, set up, and safety compliance for future reference.
Training and Safety Procedures:
Train employees on how to safely use the mezzanine, together with tips for load capability, secure access, and correct storage practices.
Maintenance and Inspection:
Establish a daily upkeep and inspection schedule to ensure the mezzanine remains secure and structurally sound over time.
Mezzanine design and installation should be carried out by skilled professionals to make sure the protection and performance of the structure. Hiring a design and construction group with expertise in mezzanine methods is essential for a profitable venture. Proper planning and adherence to rules are crucial to avoid potential points during and after set up..